Guide to Lean Manufacturing
Introduction
Lean manufacturing is a process that focuses on eliminating waste and improving efficiency in the production process. It is a system that has been used by many successful companies to reduce costs and increase profits. This guide will provide an overview of lean manufacturing and explain how it can be used to improve your business. It will cover topics such as the principles of lean manufacturing, the benefits of lean manufacturing, and how to implement lean manufacturing in your organization. Additionally, this guide will provide resources and tools to help you get started with lean manufacturing.
How to Implement Lean Manufacturing Principles in Your Business
Lean manufacturing is a production system that focuses on eliminating waste and improving efficiency. It is based on the idea that businesses should strive to produce only what is needed, when it is needed, and in the amount needed. By implementing lean manufacturing principles, businesses can reduce costs, increase productivity, and improve customer satisfaction.
1. Identify Waste: The first step in implementing lean manufacturing principles is to identify areas of waste in your business. Waste can come in many forms, such as overproduction, waiting, transportation, motion, inventory, and defects. Once you have identified areas of waste, you can begin to take steps to reduce or eliminate them.
2. Streamline Processes: Streamlining processes is essential for reducing waste and improving efficiency. This involves analyzing each step of the production process and looking for ways to make it more efficient. This could include automating certain tasks, eliminating unnecessary steps, or streamlining the flow of materials.
3. Implement Continuous Improvement: Continuous improvement is an important part of lean manufacturing. This involves regularly evaluating processes and making small changes to improve them. This could include making changes to the production process, introducing new technology, or improving the quality of materials.
4. Empower Employees: Empowering employees is essential for successful implementation of lean manufacturing principles. Employees should be given the tools and training they need to identify areas of waste and suggest improvements. This will help to ensure that employees are engaged in the process and that they are motivated to make improvements.
5. Measure Performance: Measuring performance is essential for ensuring that the changes you make are having the desired effect. This could involve tracking key performance indicators such as production time, cost, and quality. By regularly measuring performance, you can identify areas of improvement and make adjustments as needed.
By implementing these lean manufacturing principles, businesses can reduce costs, increase productivity, and improve customer satisfaction. It is important to remember that lean manufacturing is an ongoing process and that it requires commitment and dedication from all levels of the organization. With the right approach, businesses can reap the rewards of lean manufacturing and achieve long-term success.
The Benefits of Lean Manufacturing for Small Businesses
Lean manufacturing is a production system that focuses on eliminating waste and improving efficiency. It is a popular method for large companies, but it can also be beneficial for small businesses. Lean manufacturing can help small businesses reduce costs, increase profits, and improve customer satisfaction.
One of the main benefits of lean manufacturing for small businesses is cost reduction. By eliminating waste and streamlining processes, small businesses can reduce their overhead costs and increase their profits. Lean manufacturing also helps small businesses reduce their inventory costs. By reducing the amount of inventory they need to keep on hand, small businesses can save money on storage and shipping costs.
Another benefit of lean manufacturing for small businesses is improved customer satisfaction. By streamlining processes and eliminating waste, small businesses can reduce their lead times and deliver products to customers faster. This can help small businesses build customer loyalty and increase their sales.
Finally, lean manufacturing can help small businesses become more competitive. By reducing costs and improving efficiency, small businesses can offer competitive prices and better customer service than their larger competitors. This can help small businesses gain market share and increase their profits.
Overall, lean manufacturing can be a great tool for small businesses. By reducing costs, improving customer satisfaction, and becoming more competitive, small businesses can increase their profits and grow their business.
The Role of Technology in Lean Manufacturing
Technology plays an important role in Lean Manufacturing, a production system that seeks to reduce waste and increase efficiency. Lean Manufacturing is based on the principles of the Toyota Production System, which emphasizes the elimination of waste and the continuous improvement of processes. Technology is used to support these principles by providing data and analysis that can be used to identify areas of waste and inefficiency.
Technology can be used to monitor and analyze production processes in real-time. This allows for the identification of problems as they occur, allowing for quick corrective action. Technology can also be used to track and analyze production data over time, allowing for the identification of trends and patterns that can be used to improve processes.
Technology can also be used to automate processes, reducing the need for manual labor and increasing efficiency. Automation can also reduce the risk of human error, which can lead to costly mistakes. Automation can also be used to reduce the amount of time needed to complete a task, allowing for faster production times.
Technology can also be used to improve communication between departments and personnel. This can help to ensure that everyone is on the same page and that tasks are completed in a timely manner. Technology can also be used to provide feedback to personnel, allowing them to make adjustments to their processes in order to improve efficiency.
In conclusion, technology plays an important role in Lean Manufacturing. Technology can be used to monitor and analyze production processes, automate tasks, and improve communication. By utilizing technology, Lean Manufacturing can reduce waste and increase efficiency, leading to improved productivity and profitability.
Strategies for Reducing Waste in Lean Manufacturing
1. Implement a Pull System: A pull system is a method of production and inventory control that responds to actual customer demand. This system eliminates the need for excess inventory and reduces the amount of waste generated.
2. Utilize Just-in-Time (JIT) Manufacturing: JIT is a production system that focuses on delivering the right product, in the right quantity, at the right time. This system reduces the amount of waste generated by eliminating the need for excess inventory and ensuring that only the necessary materials are used.
3. Streamline Processes: Streamlining processes can help reduce waste by eliminating unnecessary steps and activities. This can be done by analyzing processes and identifying areas where waste can be reduced.
4. Utilize Automation: Automation can help reduce waste by eliminating the need for manual labor and ensuring that processes are completed accurately and efficiently.
5. Implement Quality Control: Quality control is essential for reducing waste in lean manufacturing. Quality control measures can help identify and address issues before they become costly problems.
6. Utilize Visual Management: Visual management is a system of displaying information in a visual format. This can help reduce waste by providing workers with the information they need to make informed decisions.
7. Utilize Kaizen: Kaizen is a Japanese term that means “continuous improvement.” This system focuses on making small, incremental changes that can help reduce waste and improve efficiency.
8. Utilize 5S: 5S is a system of organization and standardization that can help reduce waste by ensuring that processes are completed in an efficient and organized manner.
9. Utilize Root Cause Analysis: Root cause analysis is a method of problem solving that focuses on identifying and addressing the underlying causes of problems. This can help reduce waste by ensuring that issues are addressed at their source.
Best Practices for Implementing Lean Manufacturing
1. Establish a Lean Culture: Lean manufacturing is a philosophy that requires a cultural shift in the way an organization operates. To successfully implement Lean, it is important to create a culture that values continuous improvement and customer satisfaction. This can be done by providing training and education to employees on Lean principles, encouraging open communication, and rewarding employees for their efforts.
2. Identify Value Streams: The first step in implementing Lean is to identify the value streams in the organization. Value streams are the processes that create value for the customer. By understanding the value streams, organizations can identify areas for improvement and focus their efforts on eliminating waste and increasing efficiency.
3. Eliminate Waste: Once the value streams have been identified, organizations should focus on eliminating waste. Waste can come in many forms, such as overproduction, waiting, transportation, motion, and defects. By eliminating waste, organizations can reduce costs and increase efficiency.
4. Implement Continuous Improvement: Continuous improvement is an important part of Lean manufacturing. Organizations should strive to continuously improve their processes and products by using data-driven decision making and problem-solving techniques.
5. Measure Performance: To ensure that Lean initiatives are successful, organizations should measure performance. This can be done by tracking key performance indicators such as cycle time, cost, quality, and customer satisfaction. By measuring performance, organizations can identify areas for improvement and ensure that Lean initiatives are successful.
6. Engage Employees: Engaging employees is essential for successful Lean implementation. Employees should be involved in the process and given the opportunity to provide feedback and suggestions. This will help ensure that employees are invested in the process and that Lean initiatives are successful.
How to Measure the Success of Lean Manufacturing Initiatives
Measuring the success of lean manufacturing initiatives is an important part of ensuring that the implementation of these initiatives is successful. Lean manufacturing initiatives are designed to reduce waste, increase efficiency, and improve quality. To measure the success of these initiatives, it is important to consider both quantitative and qualitative metrics.
Quantitative metrics are those that can be measured numerically. Examples of quantitative metrics include production output, cost savings, and cycle time. Production output can be measured by tracking the number of units produced in a given period of time. Cost savings can be measured by comparing the cost of production before and after the implementation of the lean manufacturing initiatives. Cycle time can be measured by tracking the amount of time it takes to complete a given task or process.
Qualitative metrics are those that cannot be measured numerically. Examples of qualitative metrics include customer satisfaction, employee morale, and process improvement. Customer satisfaction can be measured by surveying customers to determine their level of satisfaction with the product or service. Employee morale can be measured by surveying employees to determine their level of satisfaction with their job and the company. Process improvement can be measured by tracking the number of process improvements that have been implemented since the implementation of the lean manufacturing initiatives.
By measuring both quantitative and qualitative metrics, it is possible to get a comprehensive view of the success of lean manufacturing initiatives. This will help to ensure that the initiatives are successful and that the desired results are achieved.
Conclusion
In conclusion, Lean Manufacturing is a powerful tool for businesses to reduce waste, increase efficiency, and improve customer satisfaction. It is a comprehensive system that requires careful planning and implementation, but the rewards are worth the effort. Lean Manufacturing can help businesses become more competitive, reduce costs, and increase profits. With the right guidance and support, businesses can use Lean Manufacturing to achieve their goals and become more successful.
Lean Manufacturing Resources
- Best Continuous Improvement Quotes.
- Deming, Juran and Crosby Quality Philosophies.
- How Toyota Changed Manufacturing – Lean Thinking.
- How Toyota used its Supply Chain Model to beat FORD & GM.
- John Shook Explains the Lean Transformation Model
- Kaizen – Toyota.
- Kanban explained in 60 seconds.
- Lean, Kaizen, and Continuous Improvement.
- Lean Manufacturing | A pursuit of perfection.
- Lean Manufacturing Quotes.
- Process Improvement Quotes and Blogs.
- Process Improvement: Six Sigma & Kaizen Methodologies.
- Six Sigma In Plain English.
- The Kaizen Way: ONE SMALL STEP CAN CHANGE YOUR LIFE.
- Toyota Production System Jidoka: Stopping Production, a Call Button and Andon.
- Toyota Supply Chain Management.
Digital Transformation in Supply Chain
Guide to ERP Implementations – The Good and Bad.
Top Supply Chain Certification Programs
Guide to Autonomous Vehicles and Supply Chain.
Automation Changing Supply chain
Guide to Supply Chain Planning.
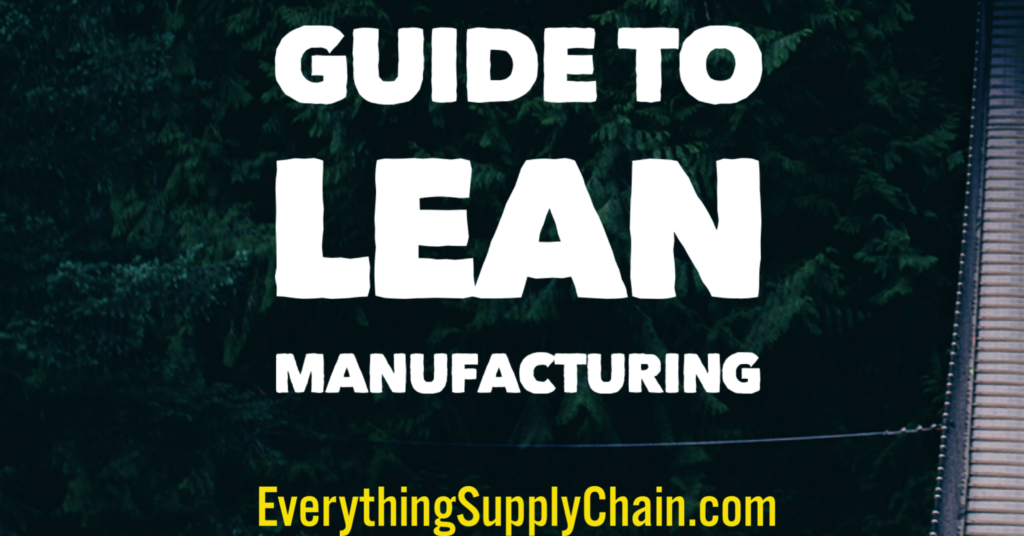