History of Continuous Improvement and Lean Manufacturing.
Evolution of Continuous Improvement and Lean Manufacturing: How It Has Changed Over Time.
Continuous improvement and lean manufacturing have been integral components of the manufacturing industry for decades. Over the years, these concepts have evolved and changed to meet the needs of the industry and the demands of the modern consumer.
The concept of continuous improvement was first introduced in the 1950s by W. Edwards Deming, an American statistician and management consultant. Deming’s philosophy was based on the idea that quality should be improved through a series of small, incremental changes. He advocated for the use of statistical process control (SPC) to identify and eliminate sources of variation in the production process. This approach was adopted by many companies and became known as Total Quality Management (TQM).
In the 1980s, the concept of lean manufacturing was introduced by Toyota. This approach focused on eliminating waste and improving efficiency in the production process. It emphasized the use of just-in-time (JIT) production, which allowed for the production of goods only when they were needed. This approach was designed to reduce inventory costs and improve customer satisfaction.
In the 1990s, the concept of Six Sigma was introduced. This approach focused on reducing defects and improving quality by using data-driven decision making. It emphasized the use of statistical analysis to identify and eliminate sources of variation in the production process.
In the 2000s, the concept of lean Six Sigma was introduced. This approach combined the principles of lean manufacturing and Six Sigma to create a more comprehensive approach to continuous improvement. It focused on reducing waste, improving efficiency, and increasing quality.
Today, the concept of continuous improvement is still evolving. Companies are now using advanced analytics and artificial intelligence to identify and eliminate sources of variation in the production process. They are also using predictive analytics to anticipate customer needs and improve customer satisfaction.
Overall, continuous improvement and lean manufacturing have changed significantly over the years. They have evolved from simple concepts to complex systems that are used to improve quality, reduce waste, and increase efficiency. As the industry continues to evolve, these concepts will continue to change and adapt to meet the needs of the modern consumer.
The Benefits of Continuous Improvement and Lean Manufacturing: How It Can Help Your Business
Continuous improvement and lean manufacturing are two of the most important concepts in modern business. They are both strategies that focus on improving efficiency and reducing waste in order to maximize profits. By implementing these strategies, businesses can become more competitive and profitable.
Continuous improvement is a process of continually improving products, services, and processes. It involves identifying areas of improvement, setting goals, and implementing changes to achieve those goals. This process can be used to improve any aspect of a business, from customer service to production processes. It is an ongoing process that requires constant monitoring and evaluation to ensure that improvements are being made.
Lean manufacturing is a production system that focuses on eliminating waste and improving efficiency. It is based on the idea that any activity that does not add value to the product or service should be eliminated. This includes activities such as overproduction, waiting, and unnecessary motion. Lean manufacturing also emphasizes the use of standardized processes and the elimination of non-value-added activities.
The benefits of continuous improvement and lean manufacturing are numerous. By implementing these strategies, businesses can reduce costs, increase efficiency, and improve customer satisfaction. Additionally, these strategies can help businesses become more competitive in the marketplace.
Continuous improvement and lean manufacturing can help businesses become more profitable. By reducing waste and improving efficiency, businesses can save money on production costs. This can lead to increased profits and improved customer satisfaction. Additionally, businesses can use these strategies to reduce their environmental impact by reducing the amount of waste they produce.
Finally, continuous improvement and lean manufacturing can help businesses become more agile and responsive to customer needs. By focusing on eliminating waste and improving efficiency, businesses can quickly respond to customer demands and make changes to their products and services. This can help businesses stay ahead of the competition and remain competitive in the marketplace.
In conclusion, continuous improvement and lean manufacturing are two of the most important concepts in modern business. They can help businesses become more profitable, reduce costs, increase efficiency, and improve customer satisfaction. By implementing these strategies, businesses can become more competitive and remain successful in the marketplace.
The Challenges of Implementing Continuous Improvement and Lean Manufacturing: What to Look Out For
Continuous improvement and lean manufacturing are two of the most important concepts in modern manufacturing. They are designed to help companies become more efficient and productive, while also reducing costs. However, implementing these concepts can be challenging. Here are some of the things to look out for when implementing continuous improvement and lean manufacturing.
1. Resistance to Change: One of the biggest challenges of implementing continuous improvement and lean manufacturing is overcoming resistance to change. People may be resistant to change because they are comfortable with the way things are, or because they are afraid of the unknown. It is important to communicate the benefits of the changes and to provide training and support to help people adjust to the new processes.
2. Lack of Resources: Another challenge is having the resources to implement the changes. Companies may not have the budget or personnel to make the necessary changes. It is important to identify the resources needed and to prioritize the changes that need to be made.
3. Poor Communication: Poor communication can lead to misunderstandings and confusion. It is important to ensure that everyone involved in the process is on the same page and understands the changes that are being made.
4. Poor Quality: Poor quality can be a major issue when implementing continuous improvement and lean manufacturing. It is important to ensure that the processes are designed to produce high-quality products.
5. Lack of Measurement: It is important to measure the results of the changes to ensure that they are having the desired effect. Without proper measurement, it is difficult to determine if the changes are having a positive impact.
These are just some of the challenges of implementing continuous improvement and lean manufacturing. It is important to be aware of these challenges and to plan accordingly. With the right resources and support, companies can successfully implement these concepts and reap the benefits.
Continuous Improvement Resources
- Best Continuous Improvement Quotes.
- Continuous Improvement Tools: Lean and Six Sigma.
- Deming’s 14 Points on Total Quality Management – TQM.
- Gemba Walk: the Path to Continuous Improvement.
- History of Continuous Improvement & Quality Gurus.
- Lean Manufacturing – Pull Systems.
- Lean Six Sigma In 8 Minutes.
- Process Improvement Quotes and Blogs.
- Process Improvement: Six Sigma & Kaizen Methodologies
- Supply Chain Today: Supply Chain Research, News, and Training.
- Toyota Way–‘The 14 Principles of the Toyota Way’.
Ways Elon Musk Might Gut the Federal Government.
Department of Government Efficiency (DOGE): Elon Musk. Good or bad?
What to expect from Elon Musk’s Department of Government Efficiency.
Introduction to Lean Manufacturing.
Process Improvement Quotes and Blogs.
5S Factory Makeover Preview.
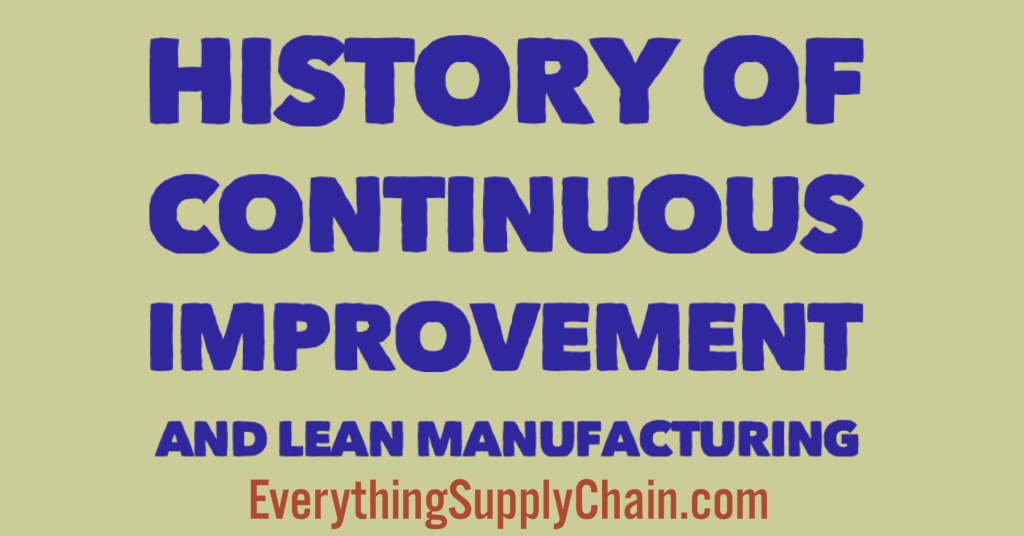