VIDEO: Process Improvement: Six Sigma & Kaizen Methodologies
Process Improvement: Six Sigma & Kaizen Methodologies
Process improvement is a method of identifying and eliminating inefficiencies and defects in a business process in order to increase efficiency, reduce costs, and improve overall performance. Two of the most widely used methodologies for process improvement are Six Sigma and Kaizen.
Six Sigma is a methodology that aims to improve the quality of a product or service by identifying and removing the causes of defects and minimizing variability in business processes. It uses a data-driven approach and statistical methods to measure and improve process performance. Six Sigma is typically implemented using a five-step process known as DMAIC (Define, Measure, Analyze, Improve, Control) which is focused on problem-solving, data analysis, and process improvement.
Kaizen, on the other hand, is a philosophy and methodology focused on continuous improvement. This approach is based on the idea that all processes can be improved upon and that improvement should be an ongoing process. Kaizen emphasizes the involvement of employees at all levels in the improvement process, using a combination of teamwork, training, and the use of visual management tools to make improvements.
Both Six Sigma and Kaizen methodologies can be applied to a wide range of industries and processes, from manufacturing and engineering to healthcare and services. Both methodologies focus on improving processes by reducing variability, which leads to a reduction of errors and defects and increase in efficiency, Kaizen tends to be more focused on the human aspect, involving and empowering people to identify, understand and improve the processes, meanwhile Six Sigma focus more on data and statistical analysis. Both methodologies can be used independently or integrated together to enhance the process improvement process.
Criticality of Process improvement
- Increased Efficiency: Process improvement identifies and eliminates inefficiencies, such as bottlenecks and redundancies. Streamlining workflows helps organizations operate more smoothly and use resources more effectively, leading to faster and more cost-effective operations.
- Cost Reduction: By optimizing processes, businesses can lower operational costs. This includes reducing waste, minimizing errors, and avoiding unnecessary steps, which collectively contribute to cost savings.
- Enhanced Quality: Improving processes helps standardize practices and reduce variability. This leads to higher quality products or services, fewer defects, and greater consistency, which can enhance customer satisfaction and reduce returns or complaints.
- Customer Satisfaction: Efficient processes contribute to better customer experiences. Faster response times, reliable service, and higher quality products or services all lead to increased customer satisfaction and loyalty.
- Employee Productivity and Morale: Streamlined processes often simplify employees’ tasks and reduce their workload. This can lead to increased productivity and job satisfaction, as employees spend less time dealing with inefficiencies and more time focusing on meaningful work.
- Compliance and Risk Management: Process improvement helps ensure that business practices adhere to regulatory requirements and industry standards. Improved processes also help identify and mitigate risks, reducing the likelihood of compliance issues or operational disruptions.
- Innovation and Growth: Efficient processes free up resources and time, allowing organizations to focus on innovation and strategic growth initiatives. Improved processes can also be a platform for adopting new technologies or expanding into new markets.
- Competitive Advantage: Businesses that continuously improve their processes can achieve a competitive edge. They can offer better value to customers, operate more efficiently, and respond more quickly to market changes than their competitors.
- Data-Driven Decisions: Process improvement often involves gathering and analyzing data to understand performance and identify areas for enhancement. This data-driven approach leads to more informed decision-making and more effective strategies.
- Long-Term Sustainability: Regular process improvement helps businesses remain adaptable and resilient in the face of changing market conditions. It supports long-term sustainability by fostering a culture of continuous learning and adaptation.
Overall, process improvement is essential for maintaining and enhancing a business’s operational efficiency, quality, and competitiveness. It’s a fundamental practice for organizations aiming to optimize their performance and achieve sustained success.
Kaizen vs Six Sigma
Process Improvement Quotes
- “Why not make the work easier and more interesting so that people do not have to sweat? The Toyota style is not to create results by working hard. It is a system that says there is no limit to people’s creativity. People don’t go to Toyota to ‘work’ they go there to ‘think’” ~ Taiichi Ohno
- “Sometimes no problem is a sign of a different problem” ~ Mark Rosenthal
- “Continuous improvement is better than delayed perfection.” ~ Mark Twain
- “A relentless barrage of “why’s” is the best way to prepare your mind to pierce the clouded veil of thinking caused by the status quo. Use it often.” ~ Shigeo Shingo
- “Good is the enemy of great. That’s why so few things become great.” ~ James C. Collins
- “An hour saved at the non-bottleneck is a mirage.” ~ Eliyahu M. Goldratt, The Goal
- “Almost all quality improvement comes via simplification of design, manufacturing, layout, processes, and procedures.” ~ Tom Peters
- “Time waste differs from material waste in that there can be no salvage. The easiest of all wastes and the hardest to correct is the waste of time, because wasted time does not litter the floor like wasted material.” ~ Henry Ford
- “Put a good person in a bad system and the bad system wins, no contest.” ~ W. Edwards Deming
- “I fear not the man who has practiced 10,000 kicks once, but I fear the man who has practiced one kick 10,000 times.” ~ Bruce Lee
- “Many people think that Lean is about cutting heads, reducing the work force or cutting inventory. Lean is really a growth strategy. It is about gaining market share and being prepared to enter in or create new markets.” ~ Ernie Smith
- “When you are out observing on the gemba, do something to help them. If you do, people will come to expect that you can help them and will look forward to seeing you again on the gemba.” ~ Taiichi Ohno
Process Improvement and Lean Blogs
- Best Continuous Improvement Quotes.
- Continuous Improvement Tools: Lean and Six Sigma.
- Deming’s 14 Points on Total Quality Management – TQM.
- End To End Supply Chain Management Process.
- Intro to Lean: What are the 7 Wastes of Lean?
- Introduction to Lean Manufacturing.
- Kaizen – Japanese Philosophy That Will IMPROVE Your Life
- Kanban explained in 60 seconds.
- Lean Kaizen DMAIC Six Sigma.
- Lean Manufacturing – Lean Factory Tour.
- Lean Six Sigma In 8 Minutes.
- Learn to Innovate Supply Chain in an Hour.
- Mapping a Value Stream to a Kanban Board.
- MIT 16.660 Introduction to Lean Six Sigma Methods. Hour video.
- Rooting Out Waste in Health Care by Taking Cue From Toyota.
- Supply Chain Quotes: Take it to the next level.
- The Best Kaizen Quotes
- The Bullwhip Effect 101.
- The Toyota Way To Lean Leadership – Keynote talk by Jeffrey Liker. 60 min video.
- What is Supply Chain Management?
- Understand Lean and Agile Supply Chain strategies.
Watch How a Lean Thinking Company Runs a Morning Meeting. 4 min video, 12.5k views.
5s Office to 5s Manufacturing. Results? Lean Production. 80k views
Lean Manufacturing – Lean Factory Tour
Total Quality Management – Deming Way. 60k views
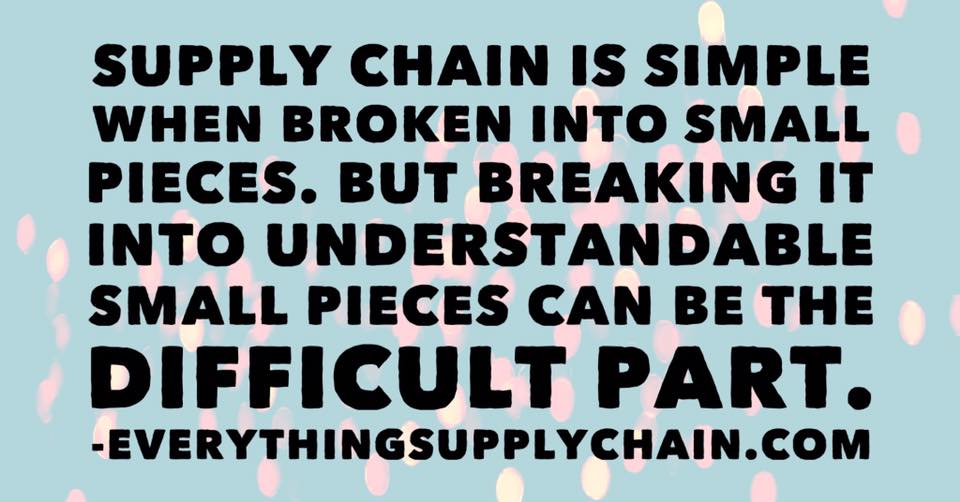
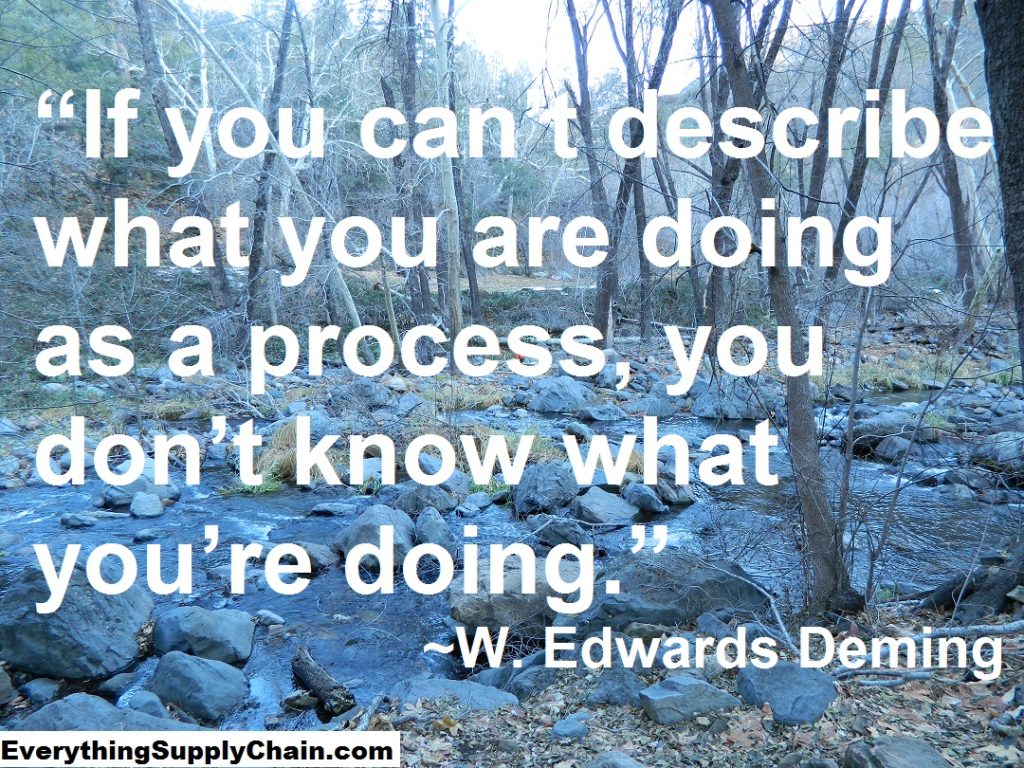