The Toyota Way To Lean Leadership – Keynote talk by Jeffrey Liker. 60 min video
The Toyota Way
The Toyota Way is how Toyota works. This is the keynote talk given by Jeffrey Liker at the Canadian Manufacturers & Exporters Lean conference in Winnipeg, Manitoba, Canada. Toyota is a great company to benchmark because there is so much information on them. Toyota has a world class supply chain and definitely worth researching. If you aren’t well versed with Toyota then do research on the Toyota Production System or TPS. A great deal of information will come up that will greatly help with supply chain optimization. Also do research on Taiichi Ohno who is the father of the Toyota Production System. You will start to uncover a great deal of information with these simple searches. Have a great day.
“The Toyota Way to Lean Leadership: Achieving and Sustaining Excellence through Leadership Development” by Jeffrey Liker and Gary Convis is a comprehensive guide on how Toyota’s renowned management principles can be applied to leadership and organizational development. The book builds on the principles established in Liker’s earlier work, “The Toyota Way,” and focuses specifically on how Toyota’s approach to leadership drives lean thinking and organizational excellence. Here’s a summary of key concepts and insights from the book:
Key Concepts:
- Lean Leadership Principles:
- Respect for People: Leaders at Toyota emphasize respect for individuals, valuing their input, and empowering them to contribute to problem-solving and continuous improvement.
- Continuous Improvement (Kaizen): Lean leadership involves fostering a culture of ongoing improvement. Leaders encourage employees to identify and solve problems, enhancing processes incrementally.
- Toyota’s Leadership Model:
- Gemba Leadership: Leaders are expected to go to the “gemba” (the actual place where work is done) to understand processes and engage with employees. This hands-on approach helps leaders grasp real issues and drive improvements.
- Developing People: Toyota invests in developing its people through mentoring, training, and coaching. Leaders are responsible for nurturing talent and ensuring employees have the skills and knowledge to contribute effectively.
- The Role of Leaders:
- Setting Vision and Direction: Leaders must articulate a clear vision and strategy, aligning team efforts with organizational goals.
- Modeling Behavior: Leaders should exemplify the principles of lean thinking and continuous improvement, setting a standard for others to follow.
- Problem-Solving: Effective leaders focus on solving problems by understanding root causes and implementing systemic solutions rather than quick fixes.
- Leadership Development:
- Mentorship and Coaching: Leaders are expected to mentor and coach their teams, helping them grow and develop their skills in line with lean principles.
- Creating a Learning Culture: Toyota promotes a culture where learning and development are integral. Leaders facilitate this by encouraging experimentation, learning from failures, and sharing knowledge.
- Sustaining Excellence:
- Embedding Lean Thinking: To sustain excellence, lean thinking must be embedded throughout the organization. This involves aligning leadership practices with lean principles and ensuring that they are reflected in everyday operations.
- Long-Term Perspective: Toyota’s approach emphasizes a long-term perspective over short-term gains. Leaders are encouraged to focus on sustainable growth and continuous improvement rather than immediate results.
Practical Applications:
- Leadership Training: Implement training programs that focus on lean principles, problem-solving techniques, and effective leadership skills.
- Gemba Walks: Encourage leaders to regularly visit the workplace to engage with employees, understand challenges, and drive improvements.
- Employee Involvement: Foster a culture where employees are actively involved in identifying problems and suggesting solutions, reinforcing the principles of continuous improvement.
Other Lean videos you may find interesting:
- 5s Office to 5s Manufacturing. Lean Production System.
- Assortment of Lean videos.
- Becoming a Lean Supply Chain Professional.
- Best Kaizen Quotes.
- Gemba Walk: the Path to Continuous Improvement.
- How Toyota Changed Manufacturing – Lean Thinking.
- Introduction to Lean Manufacturing.
- Lean Kaizen DMAIC Six Sigma.
- The Kaizen Way: ONE SMALL STEP CAN CHANGE YOUR LIFE
- Toyota vs Tesla – Supply Chain.
- Toyota Way–‘The 14 Principles of the Toyota Way’
- What is Supply Chain Management?
- Why Lean Fails.
Rooting Out Waste in Health Care by Taking Cue From Toyota
What Does Kaizen and Emptying a Dishwasher Have in Common? Watch this Video to Learn! 100k views
Toyota Supply Chain Management.
Quotes form Taiichi Ohno, father of the Toyota Production System (TPS)
“Data is of course important in manufacturing, but I place the greatest emphasis on facts.” ~ Taiichi Ohno, father of the Toyota Production System
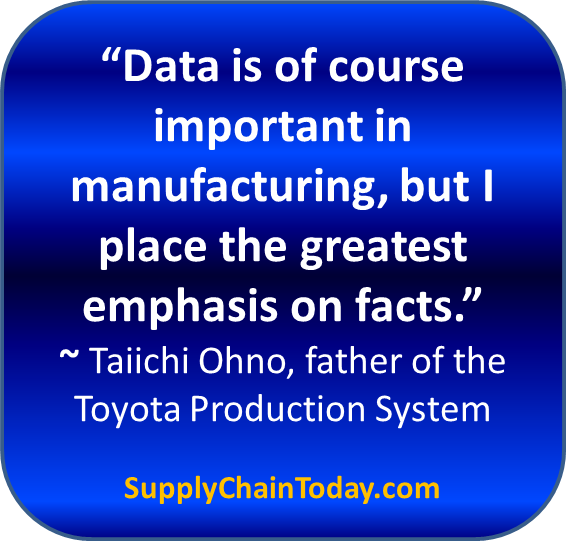
“Standards should not be forced down from above but rather set by the production workers themselves.” ~ Taiichi Ohno, father of the Toyota Production System.
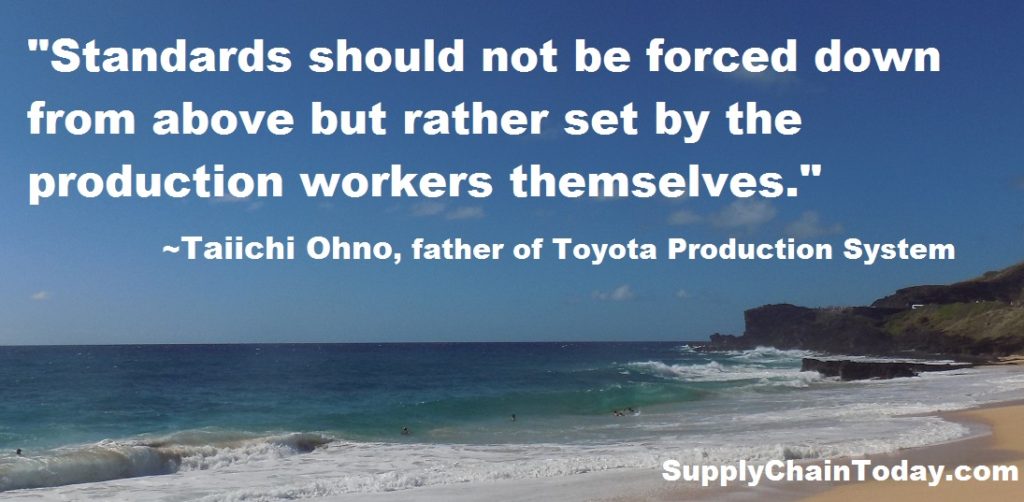
“Having no problems is the biggest problem of all.” ~ Taiichi Ohno
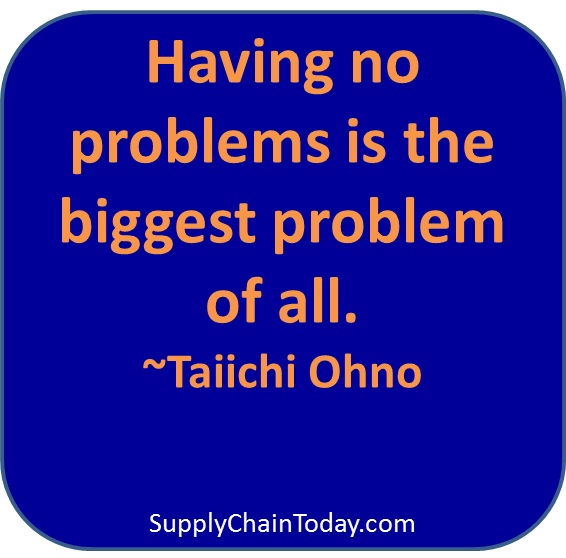
“If you are going to do TPS you must do it all the way. You also need to change the way you think. You need to change how you look at things.” ~ Taiichi Ohno
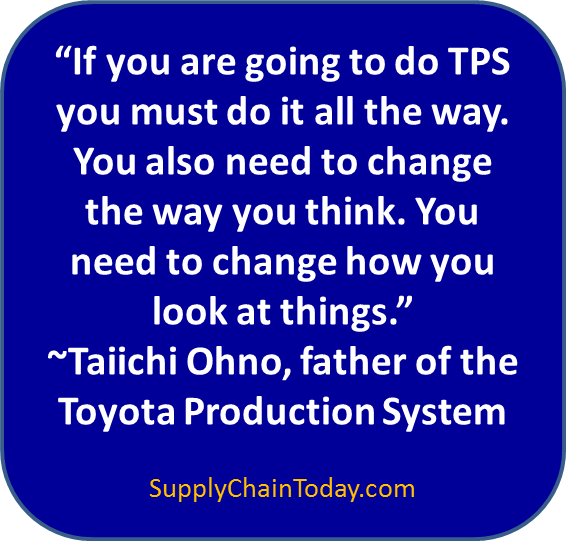