Total Quality Management: Deming Way
Total Quality Management Deming Way
“Total Quality Management Deming Way.” This lecture, from Dr. Kenneth Ragsdell’s Engineering Management 375 course for the Missouri S&T campus, discusses the Deming Way.
Total Quality Management (TQM) Deming Way Cheat Sheet
Total Quality Management (TQM) is a comprehensive approach to improving organizational performance by focusing on quality across all aspects of operations. The Deming Way, named after Dr. W. Edwards Deming, is a set of principles and practices for implementing TQM effectively.
Deming’s 14 Points
- Create a Constant Purpose for Improvement
- Establish a long-term vision for continuous improvement.
- Align organizational goals with quality improvement.
- Adopt the New Philosophy
- Embrace quality as a core value.
- Develop a culture that supports change and improvement.
- Cease Dependence on Inspection to Achieve Quality
- Build quality into the process rather than relying on end inspections.
- Focus on defect prevention instead of defect detection.
- End the Practice of Awarding Business on Price Alone
- Consider quality, reliability, and supplier capabilities, not just cost.
- Develop long-term relationships with suppliers based on quality.
- Improve Constantly and Forever the System of Production and Service
- Continuously seek ways to enhance processes and systems.
- Foster a culture of ongoing improvement and innovation.
- Institute Training on the Job
- Provide ongoing training to ensure employees have the skills needed to perform their roles effectively.
- Focus on continuous learning and development.
- Institute Leadership
- Promote leadership that fosters a supportive environment and encourages team collaboration.
- Ensure managers focus on coaching and mentoring rather than just supervising.
- Drive Out Fear
- Create an environment where employees feel safe to voice concerns and suggest improvements.
- Encourage open communication and constructive feedback.
- Break Down Barriers Between Departments
- Promote cross-functional collaboration to improve processes and solve problems.
- Foster teamwork and information sharing across departments.
- Eliminate Slogans, Exhortations, and Targets for the Workforce
- Focus on improving systems and processes rather than using motivational slogans.
- Avoid setting unrealistic targets that can demoralize employees.
- Eliminate Numerical Quotas for the Workforce and Management
- Avoid setting quotas that may encourage quantity over quality.
- Emphasize quality improvements and system enhancements.
- Remove Barriers to Pride of Workmanship
- Ensure employees have the tools, resources, and support needed to take pride in their work.
- Promote a culture of craftsmanship and quality.
- Institute a Vigorous Program of Education and Self-Improvement
- Encourage personal development and lifelong learning for all employees.
- Invest in education and training programs to improve skills and knowledge.
- Put Everybody in the Organization to Work Accomplishing the Transformation
- Engage all employees in the quality improvement process.
- Ensure everyone understands their role in achieving organizational goals.
Key Concepts
- Plan-Do-Check-Act (PDCA) Cycle: A continuous improvement cycle used to implement changes and measure their effectiveness.
- Plan: Identify an opportunity and plan for change.
- Do: Implement the change on a small scale.
- Check: Review the results and analyze the data.
- Act: If successful, implement the change on a larger scale; if not, adjust and repeat.
- Statistical Process Control (SPC): Use statistical methods to monitor and control processes, ensuring that they operate at their full potential.
- Customer Focus: Understand and meet customer needs and expectations to enhance satisfaction and loyalty.
- Continuous Improvement: Adopt a mindset of constant improvement in all areas of the organization.
- Employee Involvement: Engage employees at all levels in the quality improvement process, fostering a culture of collaboration and empowerment.
Benefits of TQM Deming Way
- Enhanced Quality: Improved product and service quality through systematic process improvements.
- Increased Efficiency: Streamlined processes and reduced waste.
- Higher Customer Satisfaction: Better meeting of customer needs and expectations.
- Employee Engagement: Greater employee involvement and morale.
Challenges
- Cultural Shift: Requires a significant change in organizational culture and mindset.
- Commitment: Needs long-term commitment from all levels of the organization.
Quality Quotes
- “Profit in business comes from repeat customers, customers that boast about your project or service, and that bring friends with them.” ~ W. Edwards Deming
- “If you do not know how to ask the right question, you discover nothing.” ~ W. Edwards Deming
- “In every crisis, there is opportunity.” ~ Chinese Proverb
- “Without changing our patterns of thought, we will not be able to solve the problems that we created with our current patterns of thought.” ~ Albert Einstein
- “If you can’t explain it simply, you don’t understand it well enough.” ~ Albert Einstein
- “It is not the strongest of the species that survive, nor the most intelligent, but the one most responsive to change.” ~ Charles Darwin
- “Quality is free. It’s not a gift, but it’s free. The ‘unquality’ things are what cost money.” ~ Philip B. Crosby
- “Quality in a service or product is not what you put into it. It is what the client or customer gets out of it.” ~ Peter Drucker
- “Quality means doing it right when no one is looking.” ~ Henry Ford
Supply Chain Resources.
- Future of the Digital Supply Chain.
- History of the Toyota Production System (TPS). Lean manufacturing.
- How Hot Dogs are made. 18.5 million views.
- How Orange Juice Is Made. Supply Chain of orange juice. 3.7 million views.
- GE Transportation: GE Supply Chain.
- IKEA’s Supply Chain.
- Introduction to Lean Manufacturing. 15 min VIDEO, 50k views.
- Kanban explained in 60 seconds. 11k views.
- Learn from great supply chain companies: Become a Supply Chain MVP.
- Six Sigma In Plain English.
- Supplier Relationship Management Best Practices with David Wohler.
- Tribute to Steve Jobs Think Different. 1.2 million views.
- Understanding and Optimizing Inventory in Supply Chains.
- Winning supply-chain technologies: The impact of technology.
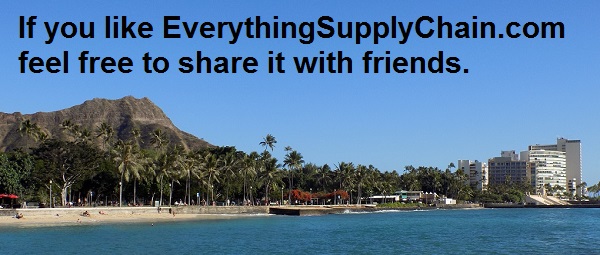
